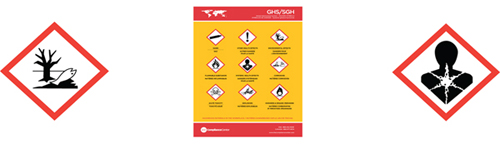
How to Prepare for an MOL Inspection
- If you have 20 or more full time, part time or seasonal employees, then you must form a Joint Health and Safety Committee. You need to have a Worker and Management rep designated and certified in Level 1 and Level 2 of safety certification plus other members. Try to get a cross section of people from across your organization.
- If you have between 5 and 20 employees, then you need to have an employee safety representative who will have to do regular safety inspections and make recommendations to the Owner or Manager.
- Once you get your safety committee up and running, you will need to meet quarterly and perform monthly safety inspections. They will then have to get all of the forms needed for the employees’ board completed and posted.
- Perform a safety audit of your entire facility, attach a priority to those safety hazards to be eliminated and establish a plan to eliminate them. Always start with the High priority items.
- Update your material safety data sheet binder. Remember that the sheets must be either issued or revised within three calendar years of this days’ date. It maybe a good time to think about disposing of any excess or unwanted chemicals. That will reduce the number of sheets to be updated and free up storage space.
- Create a shopping list of safety supply items, especially Personal Protective Equipment such as gloves, glasses, goggles, disinfectant wipes for the PPE and hearing protection and place them in a cupboard or cabinet so that they can be accessed when needed.
- Inspectors may talk to your staff and ask them if they have had the safety training required and then to prove it by examining the training records, show proof of the training and/or having the employee show the Inspector how they can safely do their job. I.E. Putting on a fall arrest harness, operating equipment, workplace violence.
- Inspectors will also be looking for definitive Heat Stress policies and training programs.
- This section is probably the most important one. Like WSIB Workwell Auditors, MOL Inspectors will now be looking for signs of an active safety program or “safety culture.” So what is a safety culture? A safety culture is an environment in a workplace where the safety of everyone in that workplace has top priority. It is successful when everyone in the workplace has the safety knowledge, training, skills and the right attitude to get the job done safely. For example:
◦ To form a safety committee with members of management and workers or to have a safety representative.
◦ Have performed and documented WHMIS training for all employees’.
◦ Bill 168 – Workplace Violence, Domestic Violence and Harassment
This legislation came into effect on June 15, 2010, and is be part of the OHS Act that impacts every business in Ontario with 5 or more employees. You are now expected to have performed a risk assessment for workplace violence, have communicated this to your employees, have met with your employees to inform them of your policies on workplace violence and harassment, trained them in workplace violence and harassment, and have put measures in place to protect your employees.
REMEMBER – The MOL expects all employers to take every reasonable precaution to protect their employees.
Your email address will not be published. Required fields are marked*